3rd Eye Fleet Health & Maintenance Software Innovation
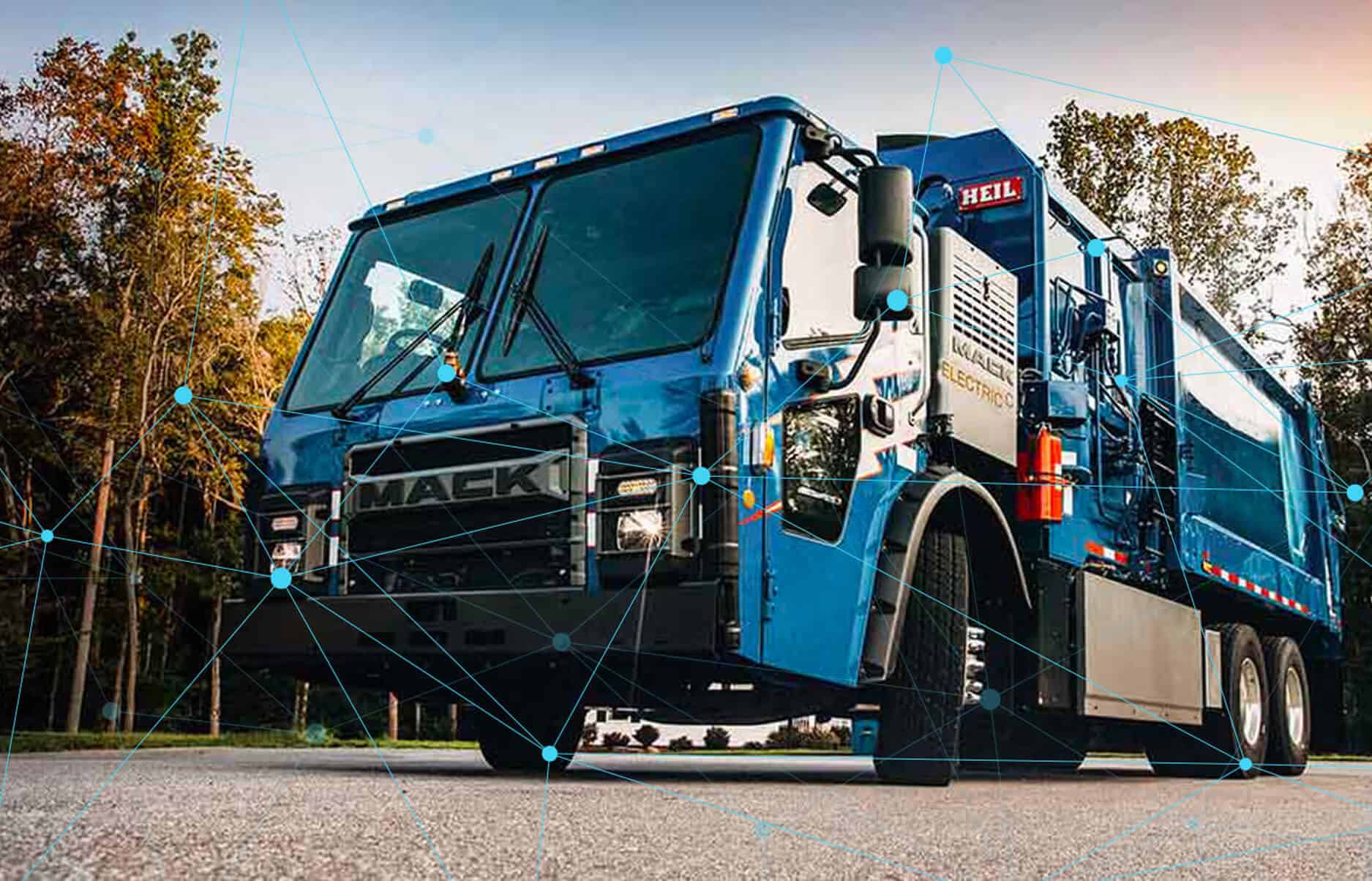
THE CROSSROADS WHERE ARTIFICIAL INTELLIGENCE AND PRODUCTIVITY MEET
Commercial vehicles are becoming more complex at a time when qualified vocational vehicle mechanics are increasingly harder to find. In fact, if you talk to the largest waste haulers in the country – it’s nearing an epidemic. The fallout from the lack of trained vehicle technicians substantially impacts a company’s bottom line – which is hardly a surprise to anyone. However, the areas hit hardest – and the longer-term impacts of poorly maintained vehicles- have a lasting ripple effect that will be felt by fleets, end-users, and equipment suppliers for years to come.
Background:
So, when Environmental Solutions Group began discussing the idea of a vehicle’s ability to communicate its health to fleet mechanics back in 2017, it raised a few eyebrows. After all, this had been tried before by some big names. And while the program names were catchy and their brands well known, at the end of the day – fleet owners were left with lots of promises, but little in terms of usable technology that positively impacted a hauler’s productivity or bottom line. In fact – at the time of this writing, the vast majority of refuse haulers continue to maintain a 12% to 15% spare ratio in their fleet, supported by maintenance shops that are only marginally equipped to service newer trucks with more complex chassis and body components. This represents a substantial investment in equipment used specifically to backfill a refuse hauling operation when front-line equipment fails.
We knew we had some heavy lifting to do regarding our vision of how the technology would work. Our team is pretty deep with regard to developing artificial intelligence (AI), but we understood that we needed to provide value at the ground level – in other words – at a level that could be interpreted and acted upon by a normal mechanic.
Eric Monsen, VP of Regional Sales
Environmental Solutions Group
Monsen said that in addition to comprehending the incoming information, the results had to measurably improve uptime if it was ever going to be viewed as useful by a fleet. And so, the bar was set high – and the journey began.
It has been said for years that refuse vehicles have the second toughest duty cycle behind that of vehicles in combat. When you consider the fact that by their very nature, garbage trucks are designed to pack the proverbial 10 lbs. of garbage into a five-pound bag, things are going to break. And up until now, when and why a garbage truck broke was anyone’s guess.
It only stood to reason that if ESG engineers could gain insight into accurately predicting when and why a truck was going to fail, it could have a huge impact on the fleet’s overall productivity. If a system could accurately identify subsystems that needed attention before a costly breakdown, maintenance could be scheduled at night, thereby avoiding a costly “truck down” situation. That vision was enough to get various members of Heil®, 3rd Eye®, and other Environmental Solutions Group companies, to begin collaborating in earnest.
TROUBLESHOOTING A MODERN GARBAGE TRUCK – THE SHOTGUN VS. THE SNIPER RIFLE
First, the joint development team looked at the current state of troubleshooting at most refuse hauling fleets. What were the issues? Where were the gaps? What did success look like, and how much would a predictive/prescriptive system cost? These were all great questions and the answers to each of them were important to understand the hurdles that would have to be overcome in order to deliver a product that would positively impact a fleet. To hit the mark, this system needed to help them to reduce their downtime, lower their parts inventory, and level load their maintenance spend by avoiding catastrophic failures.
TROUBLESHOOTING: THE ISSUES
Troubleshooting was clearly step one. With most fleets, effective troubleshooting is a dying art – due to the lack of trained mechanics that can understand the complexities of modern chassis. It’s no longer the ability of a mechanic with a good ear to easily interpret a sticky valve or leaky cylinder. It takes a significant amount of education and skill to understand a chassis’ digital “brain,” and that’s if a shop is sophisticated enough to possess the expensive diagnostic equipment that can assist in accurately troubleshooting a problem.
It’s also expensive to continually train maintenance technicians on the latest technologies – as chassis and body manufacturers are not shy about introducing new models that continually tap the latest tech trends. The reality is that in most shops, it’s a ballet of purchasing and replacing parts until the problem is resolved and the truck is back on the road. While this is ultimately successful, the expense of replacing parts that may not be faulty, combined with the extended downtime of the vehicle and the associated manpower – can be both extremely expensive and disruptive.
MCMACKINS PRESENTS AN EXAMPLE THAT HAPPENS VIRTUALLY EVERY DAY.
“A technician calls because there is no hydraulic pressure at the valve block when the pump is running. The technician has already taken several steps on their own before calling for help. First, they replaced the valve block, then they replaced the entire pump. When that didn’t work, they assumed that maybe the new pump they had just installed was bad and proceeded to replace it a second time! So, after just two days in the shop and $11,500 spent in parts and labor, they find themselves back at square one.
Personnel from the Heil Technical Service Group take the technician back to the basics, retrieving information on the type of truck, recent maintenance conducted, and any notable maintenance history. They then pull out the relevant schematic diagrams for the RCV and ask if the high-pressure filter assembly was checked. On this model, the high-pressure filter is optional – and is the only thing between the pump and the valve block. Surprised, the technician then checked the filter assembly and found that it was damaged. Replacement of the high-pressure filter assembly with labor was only $567.
TROUBLESHOOTING: THE GAPS
These situations – and their costly outcomes, became the fuel that identified the gaps this system would have to address and then prevent. The question then became, “how can we develop a mechanism that can truly look at a vehicle and predict when it will fail?” For that, a lot of analytical research needed to be conducted regarding the true cost of maintenance from two different models – one based on average maintenance costs – and the other focused on catastrophic failures. Several large national fleets agreed to share their maintenance information – which was agnostic to any particular manufacturer or chassis. This methodology was decided upon to ensure that fleet data was not skewed to any particular vendor – but rather focused purely on maintenance outcomes regarding electrical, hydraulic, and powertrain systems and components. This data would then be entered into software models that would algorithmically chart system meantime-between-failure modes to provide the “best estimate” of when a system or part would fail. This information would then be entered into a monitoring/tracking solution that could alert fleet maintenance personnel of impending service needs if/when this comprehensive system was to be created.
REDUCE SPARES. IMPROVE ASSET UTILIZATION. OPTIM-EYES
ESG President, Pat Carroll often refers to refuse collection routes as ‘factories without a roof.” In modern factories, machinery used to make products are monitored to ensure they work at peak performance to achieve optimum productivity. A Heil refuse vehicle is like a machining center in a factory – and with the monitoring of critical systems, provided by a digitally ‘connected’ truck, fleet owners can view productivity data in a similar fashion. Conversely, if the asset is not operating to expectations, productivity and/or quality is impacted. “A refuse collection vehicle that cannot start or finish its route due to a maintenance issue triggers a host of events that eat away the bottom-line profitability of the hauler and can negatively impact the relationship the hauler has with their customers,” said Carroll. “When a truck goes down, a spare has to be employed to finish the route – or other trucks need to be rerouted to handle the downtime. On the back side, the truck needs to be towed back to the shop, routine maintenance on other assets needs to be rescheduled to handle the downed truck, and manpower needs to be shifted to ensure the labor is available to fix the repair.” Carroll went on to say that in addition to the service interruption, costly spares – or extra trucks need to be on hand to take up the slack when a truck goes down. “Spares are needed to handle the “what if” scenarios, which is extremely expensive. Most of these trucks are older ‘end-of-life’ trucks that are costly to operate and maintain – specifically for the purpose of covering for a breakdown.”
Surprisingly, the team found a clue to the riddle [or at least the pathway] standing in front of them – in that their vehicles were already communicating critical data via the J1939 backbone that all Class 7 and above trucks after 2006 possess. Engineers and software developers at 3rd Eye and Dover began tapping into that language to first understand and then interpret how to develop a new predictive and prescriptive maintenance paradigm, which would become their Fleet Health & Maintenance solutions – the maintenance SaaS module under the Connected Collections umbrella of digital fleet productivity products offered by 3rd Eye.
TRANSFORMING DATA INTO INFORMATION: ENTER EYE-SITE BUSINESS INTELLIGENCE
Engineers from 3rd Eye had been working with chassis and body data passing through its digital “gateway” to the 3rd Eye cloud for several years – but the complexity of the data shared, combined with the unwieldy interface – made interpretation of the data extremely complex for end-users to benefit from.
While others in the industry threw around terms like ‘data lake’ and ‘data repository’, 3rd Eye Product Manager, Brian Ham and his team, began developing a more intuitive construct that allowed end users to custom configure the data they were interested in – into useable reports that fleet owners could act upon. This fell in line with parent company ESG’s concept of a “connected truck” and the desire to put this data to work for fleets – to allow them to make better decisions – faster. This theme gathered momentum – to eventually be the moniker for what is now ESG’s digital strategy – Connected Collections.
“We were collecting over a million bits of data per truck per day on a garbage truck and expecting a customer to comprehend this information was troublesome,” said Ham. “We realized pretty quickly that we needed to develop the means by which we could transform the data into useable information – hence the creation of Eye-Site Business Intelligence. We also wanted to make sure that our ability to interpret chassis data was not tied to one particular OEM – as so many of our customers have mixed fleets.”
With Eye-Site BI, users now have a much easier way to get the information they need to make critical business decisions. Predictively, fleet owners are provided an interface that allows them to graphically view their fleet on route – while simultaneously ascertaining the relative health of each vehicle using four colored icons. “Green” trucks are “route ready” and within the operational parameters that fleet owners outline at the onset “yellow” trucks are demonstrating low-severity maintenance concerns – and those that can be addressed at the same time as a standard scheduled PM. “Orange” and “red” alerts indicate medium and high severity maintenance conditions – which instruct personnel to address them quickly to avoid a truck-down situation. This functionality is also agnostic to the brand of chassis or power train. Using this matrix allows scheduled maintenance to be coordinated and budgeted, which ensures improved fleet uptime and reduced replacement part costs from parts that are not faulty.
FLEET HEALTH & MAINTENACE: A CENTRAL COMPONENT OF CONNECTED COLLECTIONS
As previously stated, ESG’s Connected Collections digital strategy is to provide fleet owners the ability and access to information that helps them make better decisions faster. 3rd Eye Fleet Maintenance is one of four Software as a Service [SaaS] modules that puts maintenance information at a fleet owner’s fingertips. The other modules are 3rd Eye Driver Safety and Development [safety cameras and collision avoidance radar], Positive Service Verification, and Compliance, IFTA and Road Tax software solutions [federal off-highway fuel rebates and IFTA reporting]. Each of these SaaS modules can be ordered individually – as they stand on their own. But Carroll says the magic of Connected Collections comes when they are all working together to give fleet owners the clearest assessment of what their fleet is doing.
“The easiest way to comprehend the power that Connected Collections brings to fleet owners is to look at each of the four modules as instruments. By themselves, you have solo performers that generate music. But when you add them together, you have a symphony,” said Carroll, adding, “with each module, fleet owners get a clearer picture of their fleet, their route performance, and their asset’s health. When you combine all of that and look at it comprehensively, the information provided enables fleet owners to make data-driven decisions to help their operations succeed. Simply put, we want to help our customers make better decisions, faster.”
“3rd Eye Fleet Health & Maintenance software is like having a seasoned mechanic overseeing your fleet 24/7, helping to make sure that assets are out on the street working and not in the shop or on the side of the road,” said Monsen.
For more information on 3rd Eye Fleet Maintenance Solutions or Connected Collections, contact your local Heil, Soft-Pak®, or 3rd Eye sales representative.